1.引言
飞针测试是一种在SMT(表面贴装技术)生产过程中广泛应用的测试方法,用于检测电路板上的元件和电路连接是否正常。
飞针测试设备采用可移动式探针取代传统的固定针床夹具。
在测试过程中,探针在X-Y轴移动,根据预先编排的坐标位置程序,逐点接触电路板上的测试点,进行电气性能和功能测试。
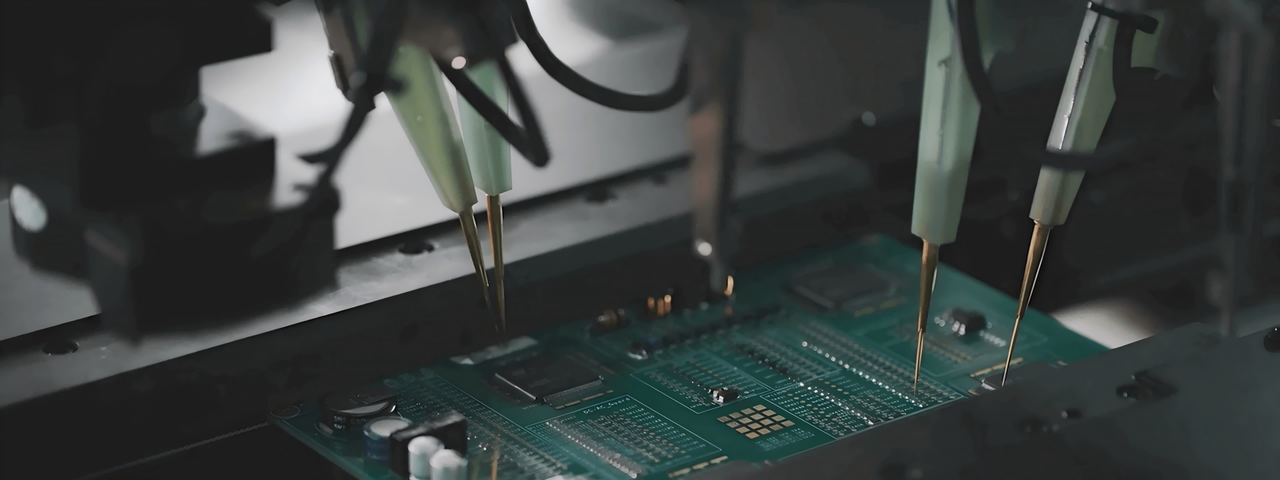
2.测试尺寸限制
最大可测PCBA尺寸500 * 410mm;最小可测PCBA尺寸50mm*50mm;PCBA厚度0.6mm~6mm;最大元件高度60mm
3.可测试的元件
- 电阻、电容、电感等:飞针设备可以检测这些元件的值是否在规定范围内,以及是否存在开路或短路的情况,从而发现制造工艺中的缺陷,如焊锡短路、元件插错、漏装等。
注:最小可测试封装元器件:0201;电阻可测量范围(1Ω~1GΩ);电容可测量范围(10pF~1F);电感可测量范围(10uH~1H)
- LED、二极管、三极管、场效应管等:飞针设备可以测试其电气特性和功能,通过施加正向和反向电压,例如测量LED和二极管的正向压降,例如测量三极管和场效应管的导通状态和放大特性,确保其在电路中能够正常放大信号。
- 集成模拟IC:飞针设备可以测试引脚开路、短路以及部分功能测试等。通过 IC 的对地二极管测试,能够有效检测 IC 引脚的焊接质量和引脚状态及连接情况,准确判断是否存在虚焊、元件方向错误等问题,确保 IC 在电路中的可靠性和稳定性。
- LDO、继电器、光耦等:飞针设备可以模拟信号源,测试其是否满足本身电源控制、信号传输的功能。例如,通过施加不同的输入电压,测量LDO的输出电压,判断其是否能够稳定地提供所需的电压。对于继电器和光耦,可以测试其控制信号的输入和输出,确保其能够正常控制和传输信号。
- 滤波器、保险丝、开关、连接器、TVS等:飞针设备可以检测这些元件的电气性能和连接情况,例如滤波器、保险丝,可以检测其在直流情况下的导通情况,确保其在电路中的正常工作。对于开关和连接器,飞针设备可以测试引脚短路情况,确保其连接可靠,避免因连锡导致的电路故障。
4.不可测试的元件
- BGA封装元件:BGA封装元件的引脚位于底部,飞针测试难以准确接触每个引脚进行测试,建议采用专业的测试设备或技术,如X射线检测等,以确保其焊接质量和电气性能。
- 集成数字IC:集成数字IC通常具有复杂的逻辑功能和大量的引脚,其内部电路结构复杂,信号传输速度快,且对测试设备的精度和稳定性要求极高。
- 晶闸管:晶闸管是一种具有特殊触发特性的半导体器件,其导通状态不仅取决于阳极和阴极之间的电压,还受到门极触发信号的控制。飞针设备难以准确模拟晶闸管的触发条件和工作状态,因此无法有效测试其电气性能和功能
- 运算放大器和比较器:这类模拟器件需要特定的工作条件,比如供电电压、输入信号、反馈回路等,才能正常工作。而飞针测试机通常只能进行静态测试,比如检查焊接是否良好、引脚是否短路或开路,无法提供动态的工作电压或信号输入。
- 固态继电器:通常需要高电压和大电流的负载环境来测试其开关功能,而飞针测试机可能只能提供低电压和小电流的测试信号,无法模拟真实工作条件。因此,无法让固态继电器正常切换或承载负载,导致测试不准确。
- 大型、形状不规则元件:大型或形状不规则的元件,其测试点难以准确定位,飞针测试可能无法覆盖所有测试点,导致测试不准确。
- 其他:对于元件引脚功能比较特殊,或者本身功能比较特殊的元件,例如红外元件、压敏/光敏电阻、霍尔元件、传感器类元件、射频元件、声学元件、MEMS器件等,飞针测试机无法模拟特殊元件工作所需的外部激励或环境条件,并且无对应的检测条件,无法对此类器件的功能进行准确的测试。
5.可规避的风险
- 生产缺陷:通过飞针测试可以在生产过程中及时发现电路板上的缺陷,如元件焊接不良、缺失、短路、开路、反向等,避免这些缺陷流入下一生产环节。
- 设计问题:通过飞针测试可以发现电路设计中存在的问题,如元件布局不合理、电路连接错误等,为设计改进提供依据,提高产品的可靠性和稳定性。
- 元件质量问题:通过飞针测试可以检测元件的电气性能和功能,确保元件的质量符合要求,避免因元件质量问题导致的电路故障。
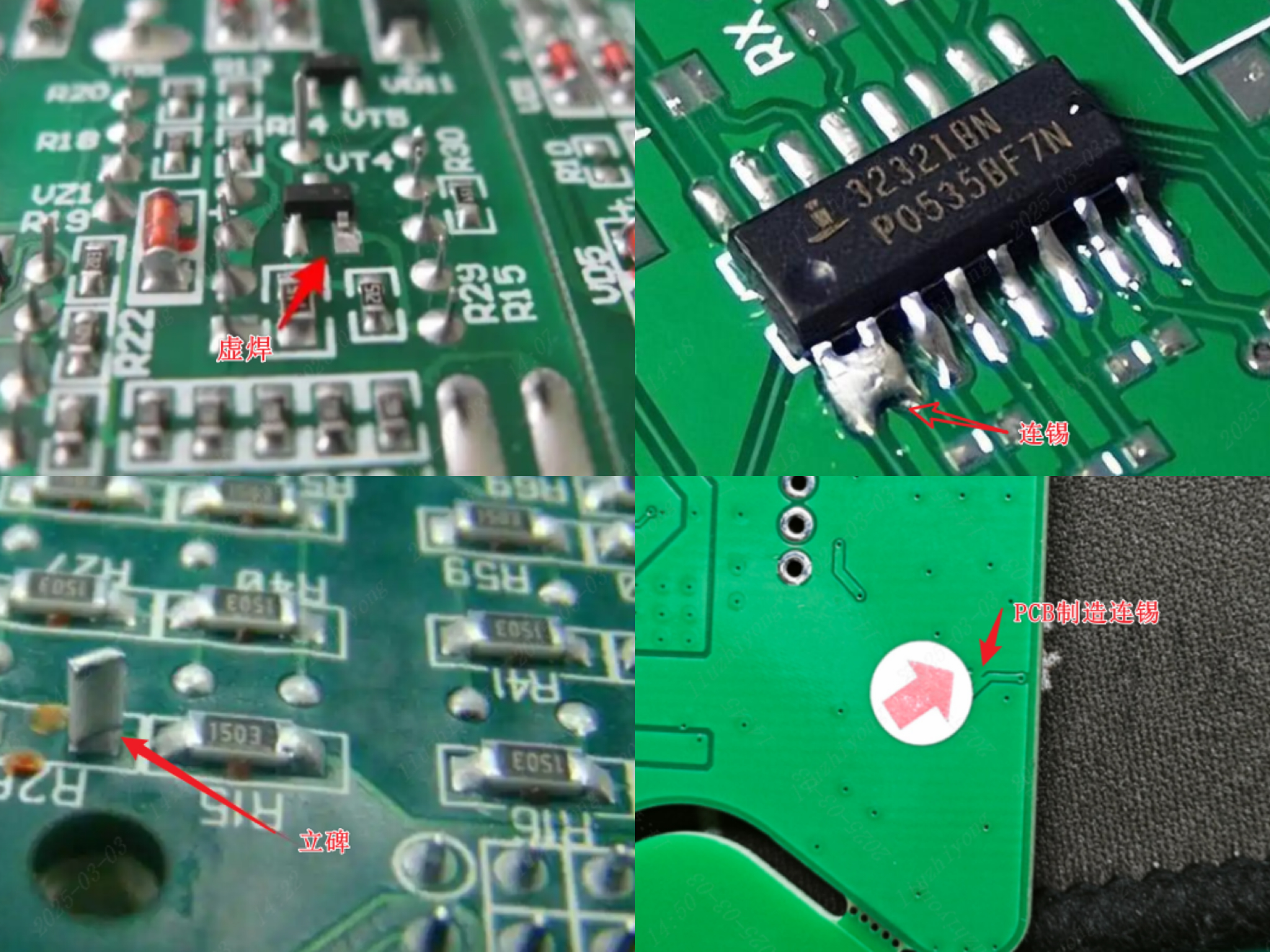
6.测试工序安排
在SMT贴片工序-AOI工序完成之后,在插件工序前测试
为什么选择在插件工序前进行SMT飞针测试?
- 早期发现缺陷:插件前进行测试可以尽早发现SMT阶段的缺陷,如元件焊接不良、短路、开路等。这样可以避免将有问题的PCB板送入插件工序,减少后续的返工和报废成本。
- 简化测试流程:在插件前进行飞针测试,可以避免插件后因元件密集和复杂性增加而带来的测试困难。飞针测试的灵活性和高精度使其能够在插件前有效检测各种缺陷。
- 降低维修成本:如果在插件后发现缺陷,维修时需要拆卸和重新焊接插件,这会增加维修的复杂性和成本。而在插件前发现并修复问题,可以大大降低维修成本。